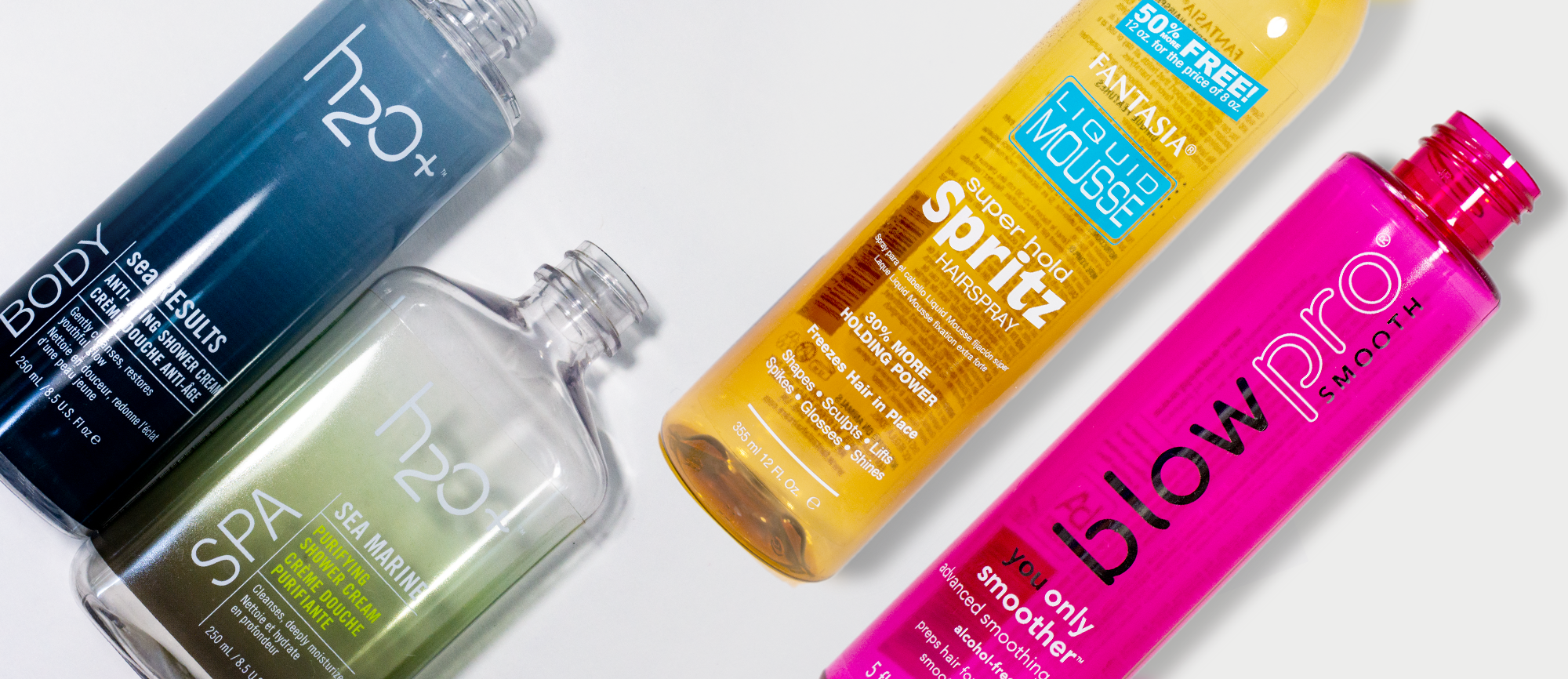
Labeling for Containers
ABOUT Labeling for plastic containers
Labels are one of the easiest ways to convey lots of precise information on a package or container. Labels convey important product details and industry regulations in a manner that is consistent with the company’s visual identity. Labels have been widely used since the commercialized production of paper and labeling remains a staple in the printing industry today.
“Labels convey
lots of
information
precisely with
infinite
finish options.”
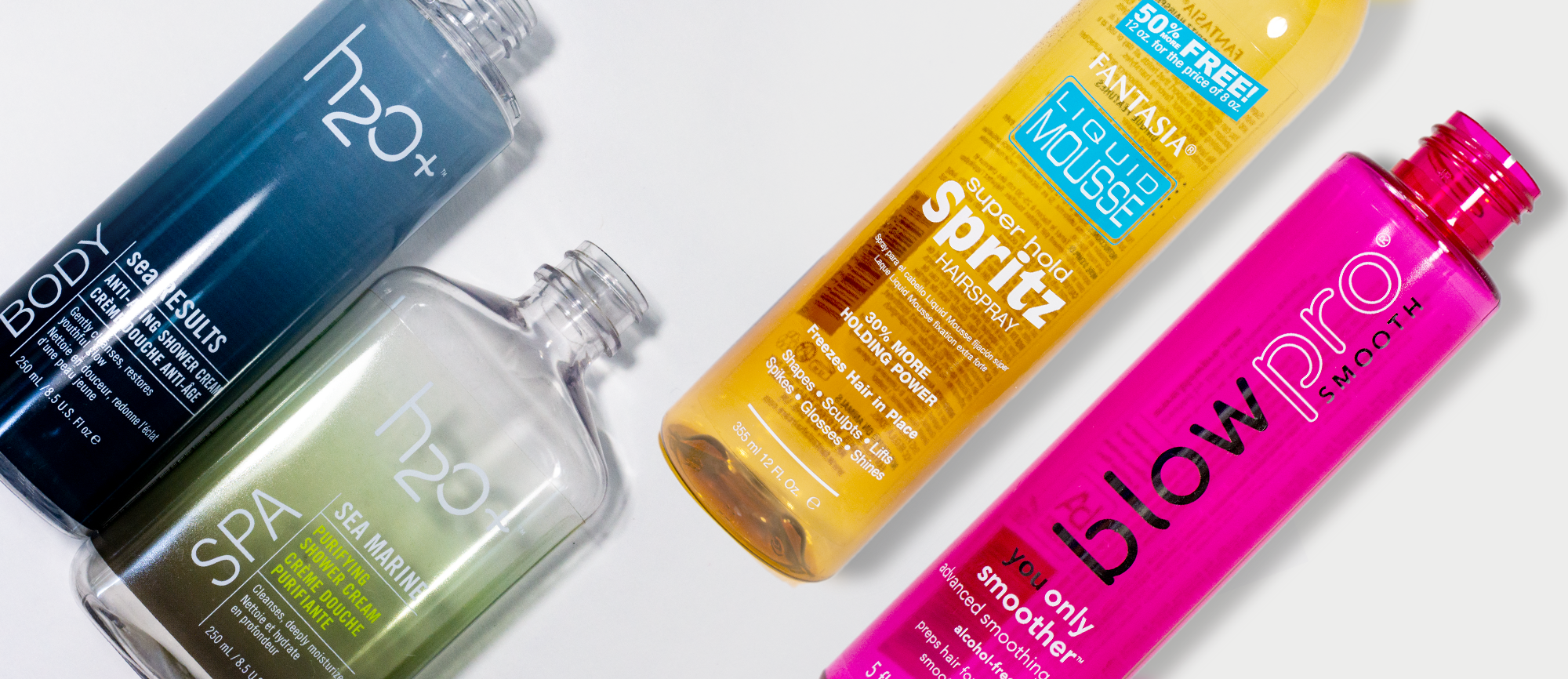
Sample Container Labeling Projects
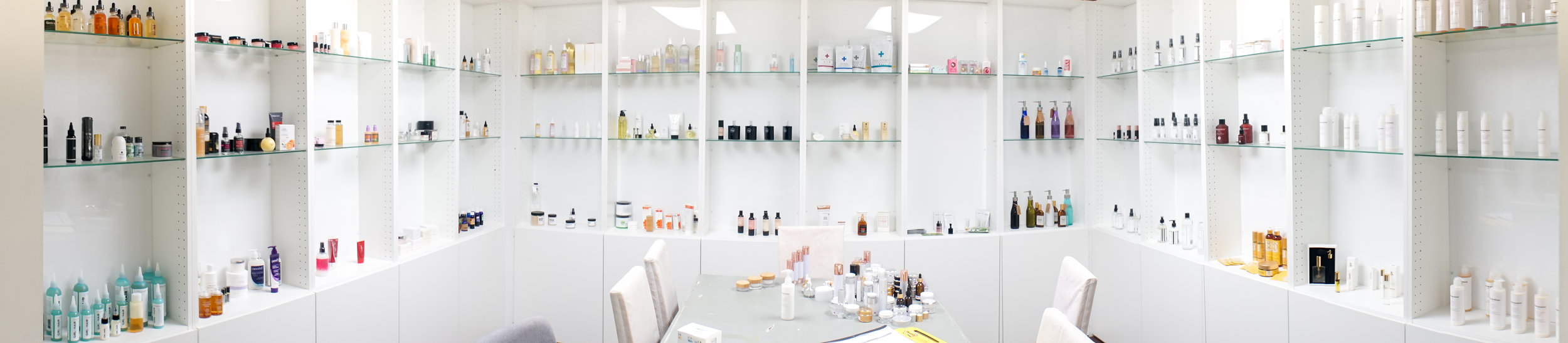
How
The Labeling Process
Labeling involves a two-step process grouped into one. First, the design for the label is created and digitally printed. Next, the labels are trimmed down to size and applied to a container with the selected adhesive. There are a number of paper finishes to pick from including permanent matte litho labels, semi gloss litho labels, and removable matte litho labels. Specialty papers are also available for projects that require superior resistance to moisture, sunlight, extreme temperatures, and wear. As with all other large scale bottle decorating processes, the labeling process can be fully or partially automated.
Clear
Industrial Container Labels
A key benefit to using labels is the ability to fit more information into a smaller area than any other printing process. The font size can be minimized without compromising the legibility or design of the label. This feature is especially important in the industrial sector where product ingredients must be clearly identified and consumer warnings are highly regulated. Coupled with wear-resistant finishes, industrial product labels are made to last as long as the container’s contents.
Color
Multi-colored Labels
Today’s printing technologies open the door to infinite possibilities in the colors and visual effects you can create with labels. Printed labels allow for exceptional complexity and intricacy in the design. Plus, when printing multiple colors, labeling is faster and more cost-effective than other container decorating processes. Labeling is a great option for companies who would like to use a wide variety of bright colors in their label designs.
Finish
Packaging & Labeling with Specialty Finishes
Labels come in a variety of finishes to choose from, such as gloss or matte varnish, gloss or matte laminate, soft touch, holographic, and embossed. The most common finish is the varnish which coats the entire label with a protective layer that can have a magazine gloss sheen or a matte, subdued yet professional look. For added durability, there is the option to laminate the label. Laminated labels have the added benefit of thicker protection and they are available with the same finishes as varnish. Laminated labels are especially suited for products exposed to UV rays, water and daily wear.
The Soft Touch label has a velvety finish that adds subtle sophistication to your products. The unique feel draws consumers in to touch and feel the product, while the coating also resists fingerprints. The holographic finish also attracts the consumer’s eye, but with brilliant rainbow-colored visuals that appear to jump off the paper. Lastly, embossing is a finish that makes the design rise up from the surface. Embossing is commonly used on drink labels such as premium beers and wines to add another level of distinction and age to the brand image.
Drink
Wine Bottles, Cans and Beer Labels
Did you know that over 4 billion bottles of wine consumed each year in the US? There’s no doubt that drink labels are one of the most used applications of printed labels. Labeling is the standard method for decorating wine and beer bottles due to its lower cost. Labels can be created with small production runs, and additional labels can be produced on an “as needed” basis. Additionally, with many wineries and breweries carrying multiple lines using the same bottles, it is more cost efficient to produce multiple printed labels than it is to create new screens or stamps for each design.
Trend
On Trend: The No-Label Look
Although the typical no-label look is often created by directly screen printing onto a glass or translucent plastic label, the same look can be achieved with a clear label. Using an ultra-clear film, labels can be printed and adhered to the product for a similar no-label effect. This labeling trend is perfect when brands are trying to emphasize the quality of their products by showing it through the packaging.
Versus
Screen Printing vs Labeling
Labels have several features that can make it a better option for your project, as opposed to screen printing. The setup costs for labeling are significantly less than screen printing or pad printing. Plus, there is the ability to apply specific dates and seasonal designs to production runs, since the labeling process has separate steps for design and application. This is especially useful in the food industry where seasonality can drive design and timely promotions.